Im Zusammenhang der Begriffe „Industrie 4.0“ bzw. „Industrial Internet of Things (IIoT)“ hört man häufig auch den Begriff der „Digitalen Fabrik“. Man meint damit, dass man mithilfe eines Modells (der Digitalen Fabrik) verschiedene Informationen, Abläufe, Methoden einer realen Fabrik abzubilden versucht. Das Ziel ist dabei, Abläufe einer realen Fabrik – von der Entwicklung und Planung der Produkte, über die Produktion derselben bis hin zur Auslieferung an den Kunden – mit Hilfe der IT zu planen, zu simulieren, zu betreiben bzw. zu optimieren.
Maschinendaten als Basis für Echtzeitvisualisierung
In einer Digitalen Fabrik stehen beispielsweise Daten, die während der Produktion anfallen, jederzeit online zur Verfügung. Diese werden mit geeigneten Sensoren erfasst und können digital weiter verarbeitet werden. Dabei stehen die wichtigsten Fertigungsdaten oftmals bereits bei einfachen Steuerungen zur Verfügung. So können Maschinensteuerungen im einfachsten Fall folgende MDE-Signale (Maschinendatenerfassungs-Signale) online zur Verfügung stellen:
- Maschine rüstet!
Die Maschine wird aktuell eingerichtet. - Maschine läuft!
Ein Arbeitsgang ist auf der Maschine angemeldet und wird aktuell bearbeitet. - Maschinenfehler!
Ein Arbeitsgang ist auf der Maschine angemeldet, kann jedoch aufgrund eines (nicht näher definierten) Maschinenfehlers aktuell nicht bearbeitet werden. - Ein Teil, ein Hub etc. wurde produziert!
Die Maschine hat für ein Teil oder einen Satz von Teilen den Arbeitsgang komplett abgearbeitet.
Allein diese wenigen MDE-Daten können dazu dienen – im Zusammenhang mit einem MES-System – den Fertigungsprozess jederzeit transparent zu gestalten. Die Herausforderung besteht dabei, diese Online-Daten dem Fertigungsprozess zuzuordnen, d. h. diese MDE-Daten müssen in Korrelation zu Fertigungsdaten aus dem ERP-System gebracht werden. Damit ist der erste Schritt Richtung Digitaler Fabrik bereits getan!
HINWEIS: Moderne Maschinensteuerungen liefern normalerweise eine Vielzahl mehr Daten. So können z. B. meist die Maschinenfehler genauer klassifiziert werden oder die Steuerung kann Daten liefern, ob ein Teil IO oder NIO ist etc.
Mithilfe der Online-MDE-Daten können bereits folgende Aussagen zum Fertigungsprozess gemacht werden:
- Auf welcher Maschine läuft welcher Fertigungsauftrag?
- Welchen Zustand hat aktuell der Fertigungsprozess (z. B. „Maschine wartet auf Arbeit“, „Maschine steht“, „Maschine wird gerüstet“, „Maschine produziert“)?
- Wie ist der aktuelle Fertigungsfortschritt (Wie viele Teile sind mit welchem Zeitaufwand produziert worden)?
Darüber hinaus können mit diesen Daten die Status der einzelnen Maschinen bzw. Fertigungszellen protokolliert und KPIs (Key Performance Indicators – z. B. OEE) generiert werden.
Wie kommen die Maschinensignale ins MES?
Es gibt mehrere Möglichkeiten erfasste MDE-Signale ins MES zu überführen. Diese sind u. a. abhängig vom Steuerungstyp, Alter der Maschine bzw. Zugriffmöglichkeit der MDE-Signale. Wichtig dabei ist, dass diese Signale zeitnah über das vorhanden Netzwerk an den MES-Server übertragen werden. Nachfolgend beispielhaft einige Möglichkeiten:
⇒ Anbindung über ein IO-Modul
Voraussetzung: Der Anwender oder Maschinenhersteller kann die Signale (möglichst potenzialfrei) zur Verfügung stellen. Die Signale werden durch das IO-Modul erfasst und über einen Netzwerkanschluss dem MES-Server zur Verfügung gestellt. Dies stellt eine sehr einfache und preisgünstige Art der Erfassung von MDE-Signalen dar.
⇒ Direkte Anbindung an die Maschinensteuerung
Lässt die Steuerung ein direktes Auslesen von Datenbausteininhalten zu (z. B bei SIEMENS-Steuerungen vom Typ S7) und weiß der Anwender, in welcher der Datenbausteine sich die notwendigen Informationen befinden, kann dies ein sehr sinnvoller Weg sein, die Daten ans MES zu übertragen.
⇒ Signalbereitstellung über OPC UA oder MQTT
Hat der Anwender die Möglichkeit MDE-Signale über steuerungsneutrale Nachrichtenprotokolle, wie OPC/UA oder MQTT, zur Verfügung zu stellen, ist dies eine weitere innovative Möglichkeit MDE-Daten dem MES-Server bereit zu stellen. Der Vorteil ist, dass es in diesem Fall keine spezielle Lösung für jede anzubindende Maschine geben muss.
Auswertungsmöglichkeiten der MDE-Daten
Die online erfassten MDE-Daten werden im MES mit den Daten des gekoppelten ERP-Systems verknüpft und stehen für Auswertungen zur Verfügung. Diese können nun in verschiedenster Form visualisiert werden.
In einer Maschinenübersicht im MES sehen die fertigungsverantwortlichen Mitarbeiten (Schichtführer, Meister, Fertigungsleiter etc.) sofort die Zustände der Maschinen inklusive wichtiger Fertigungskennzahlen anhand zugeordneter Farben. Diese Mitarbeiter haben also sofortige Informationen der wichtigsten Daten der Fertigungsprozesse zur Maschine.
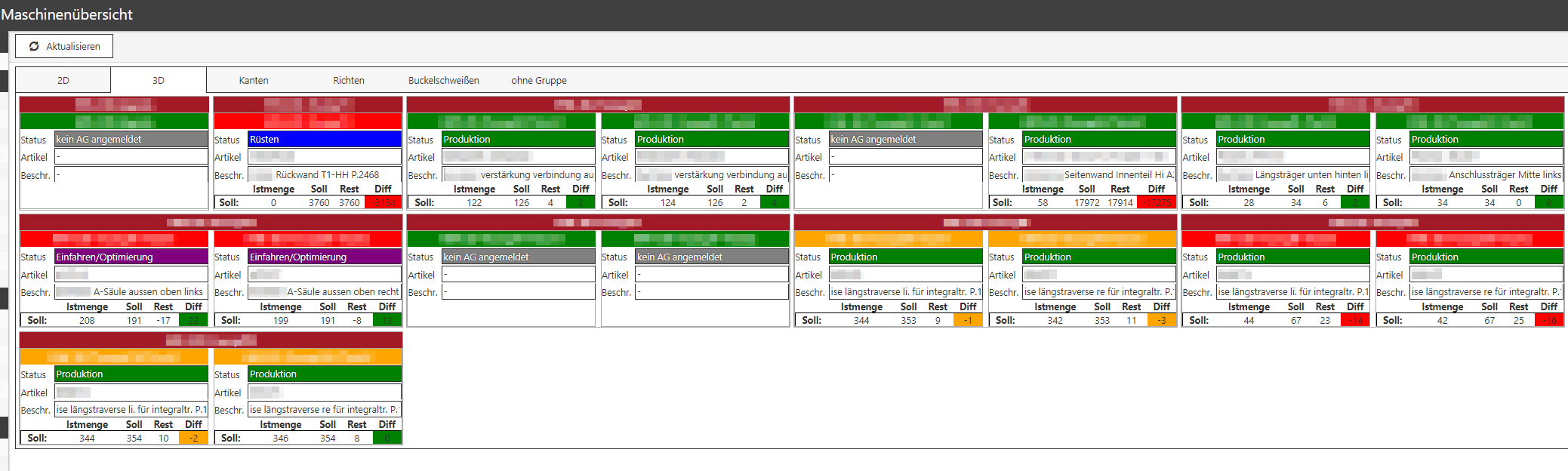
Die Darstellung der Maschineninformationen kann auch direkt in ein Fabriklayout eingeblendet werden.
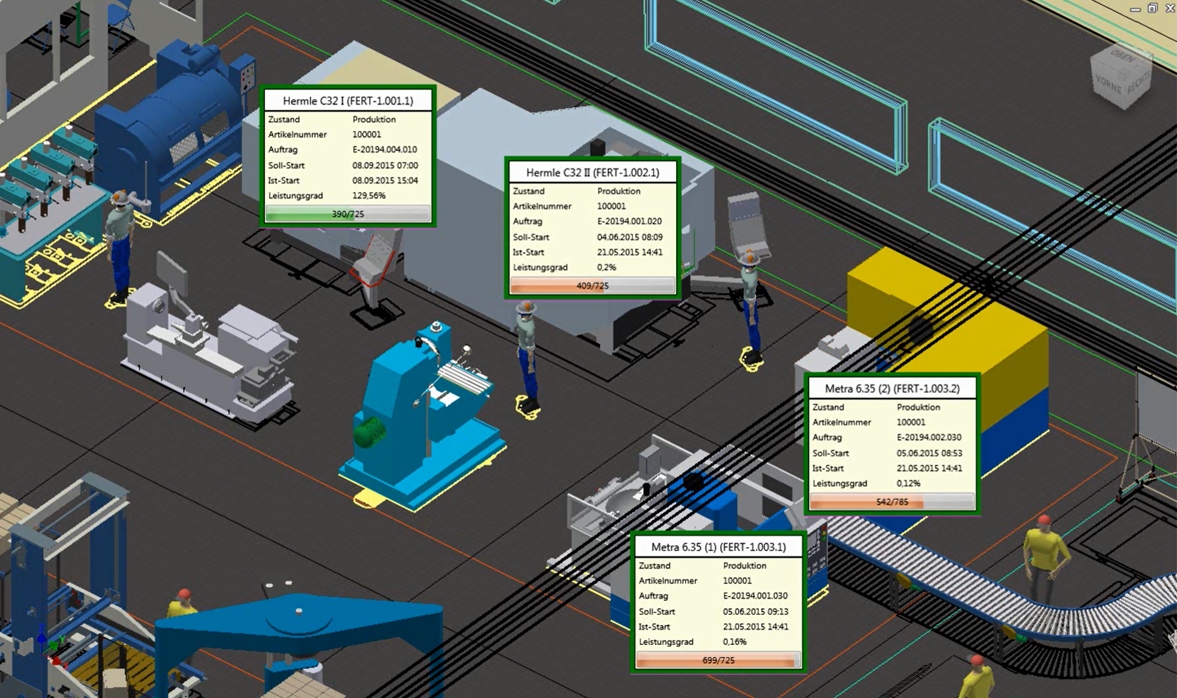
In Form eines Zeitstrahls können die Zustände von Maschinen zeitlich abhängig dargestellt werden. Ggf. können hierbei zusätzlich noch allgemeine, unklassifizierte Maschinenstörungen zugeordnet werden.
Dabei steht zu jeder selektierten Maschine sofort der Zustand derselben im zeitlichen Kontext.
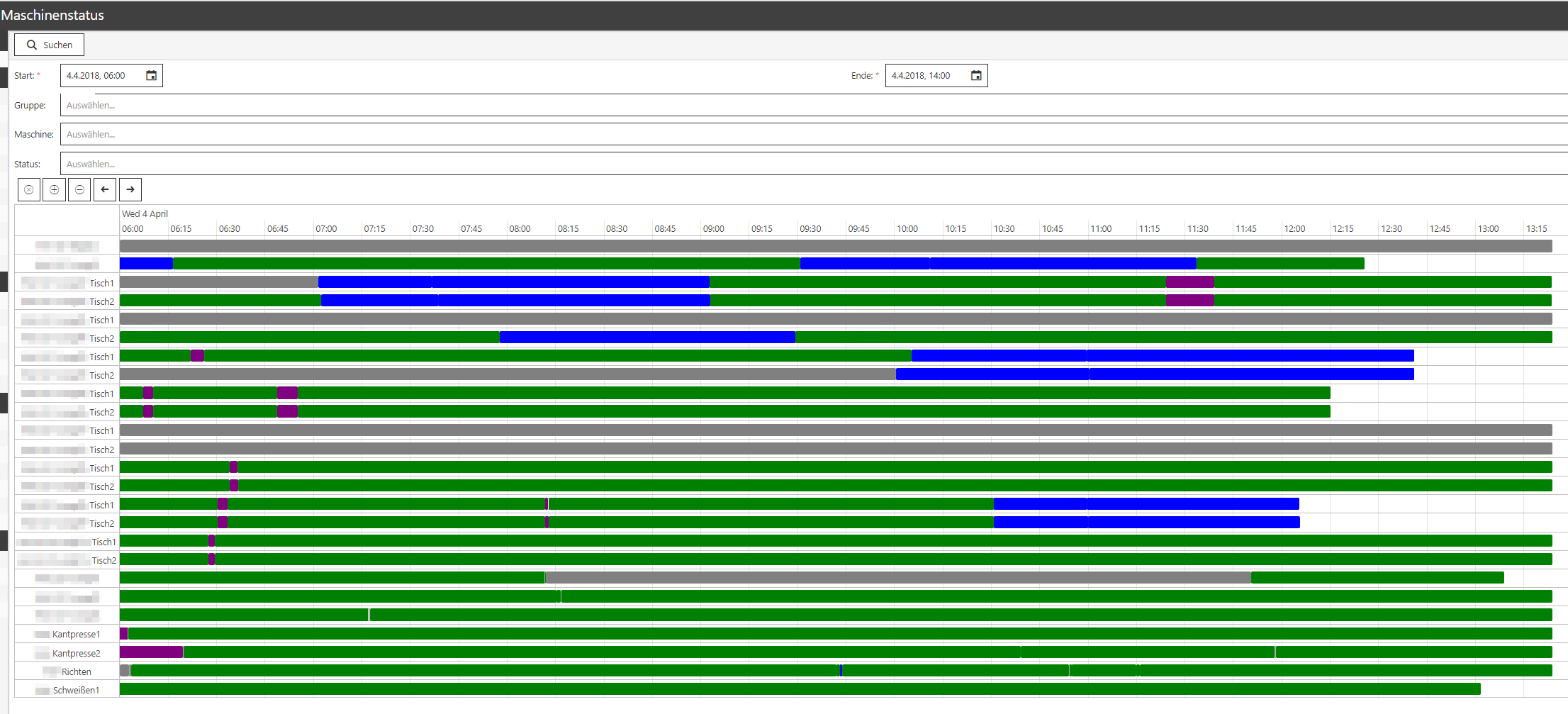
Die erfassten Maschinenzustände können auch dazu dienen, diese in Paretoanalysen über beliebige Zeiträume auszuwerten. Dabei werden die Zustände mit ihren Dauern zeitlich absteigend sortiert dargestellt.
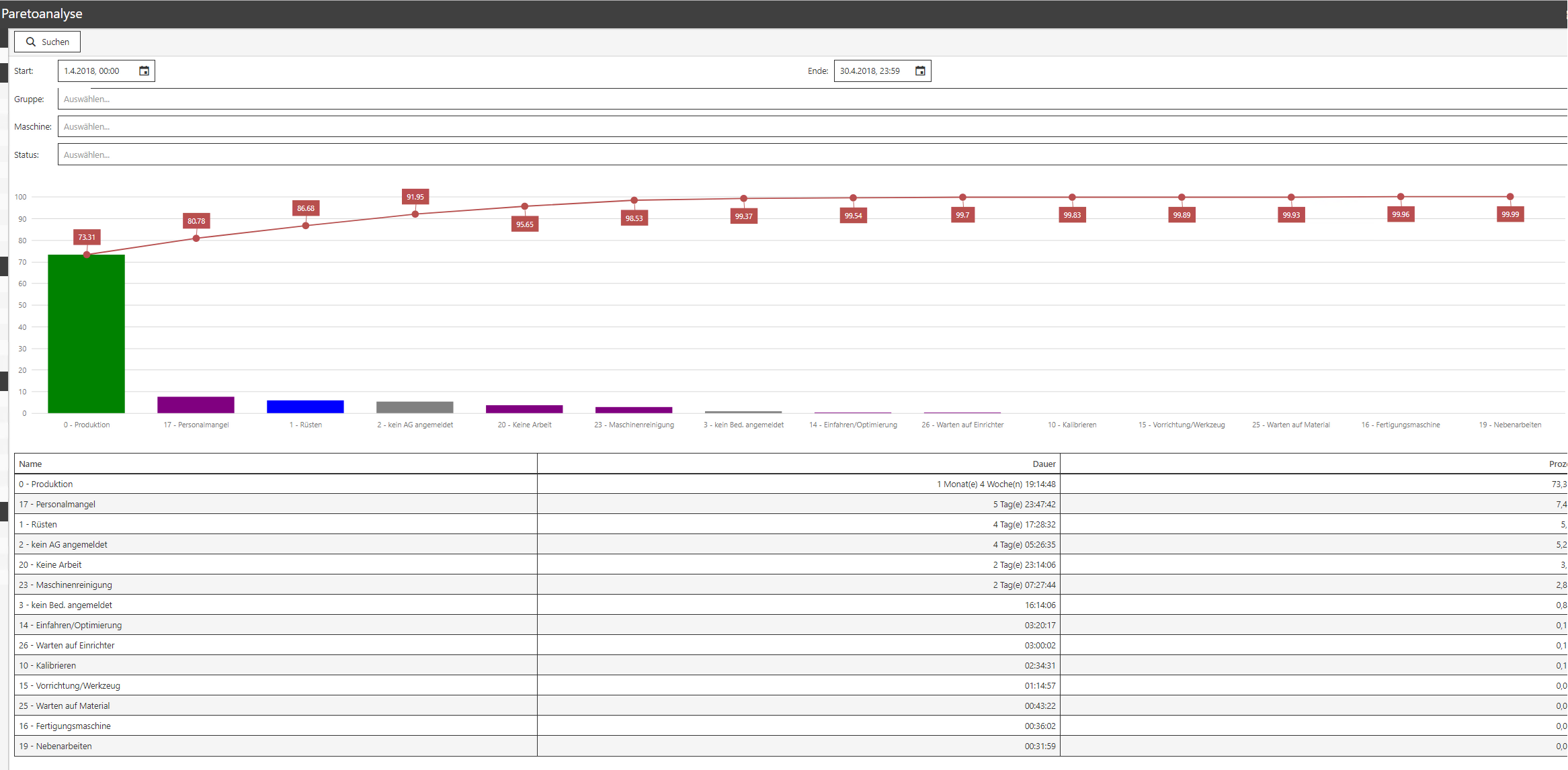
Mehrwerte einer Echtzeitsimulierung von Fertigungsdaten
Die Informationen, die die Maschinen während der Fertigung erzeugen, stehen zentral zum Zwecke der Visualisierung und Auswertung zur Verfügung.
Die MDE-Daten stehen online zur Verfügung und werden in Korrelation mit anderen Daten, z. B. Fertigungsdaten aus dem ERP/MES, gestellt.
Maschinenstörungen werden schnell erkannt und können als Trigger für ein Frühwarnsystem dienen. Damit werden verantwortliche Mitarbeiter zeitnah informiert und es können schnell entsprechende Gegenmaßnahmen eingeleitet werden.
KPIs der Fertigung können mit Maschinenbezug erstellt werden.