Eine durchgängig digitalisierte Prozesskette lebt davon, dass alle Abläufe im Unternehmen digital miteinander verbunden sind: Also von der ersten Konstruktionsidee bis zur Planung der Fertigung, von der Live-Überwachung des Produktionsablaufs bis hin zur automatisch ausgelösten Störmeldung an der Smart Watch des Technikers. Das Ziel ist es, Prozesse medienbruchfrei zu gestalten, um Fehlerquellen zu vermeiden und Potenziale aufzudecken.
Maschinendaten: Nachteile der manuellen Erfassung
Die effiziente Ausnutzung der vorhandenen Ressourcen wie Maschinen und Personal, war in der Fertigungsindustrie schon immer ein wichtiges Thema. Das hat in den letzten Jahren noch einmal rasant an Bedeutung zugenommen.
Leider stellen wir in der Realität häufig fest, dass zwischen dem ERP-System und der Produktion (also ganz speziell den Maschinen im Unternehmen) Informationen manuell ausgetauscht werden. Die manuelle Rückmeldung durch den Werker hat allerdings drei bedeutende Nachteile:
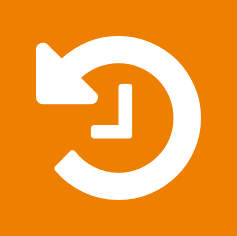
Es gibt immer einen Zeitverzug.
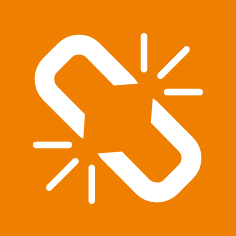
Es gibt immer subjektiven „Interpretationsspielraum“, was zu Ungenauigkeiten führt (z. B. die Einschätzung von Störgründen).
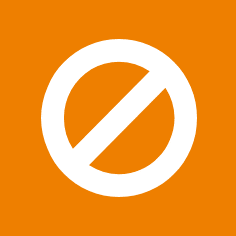
Es können Fehler passieren – das ist menschlich – wie z. B. bei der Mengen- oder Ausschusserfassung. Ein exaktes Nachverfolgen der Produktion von Produkten (oftmals mit Protokollierung von Parametern) wird aber immer wichtiger, um zum einen Kundenanforderungen erfüllen und zum anderen Schwachstellen und Optimierungspotenziale im eigenen Produktionsprozess aufdecken zu können.
Automatische Datenerfassung führt zu mehr Transparenz in der Auftragsbearbeitung
In jedem Fertigungsprozess und an jeder Maschine fallen zwangsläufig Daten an. Es macht also Sinn, diese für eine Kalkulation der Ist-Kosten und zum Transparentmachen der Prozesse bzw. deren Optimierung auch zu nutzen und auszuwerten. Warum soll sich der Werker mit Meldetätigkeiten beschäftigen, wenn die Informationen an der Maschine bereits vorliegen?
Eine praxisgerechte MES-Lösung verknüpft dabei die Auftragsdaten aus dem ERP-System direkt mit den realen Fertigungsdaten bzw. Maschinendaten. Der Werker startet z. B. einen Arbeitsgang am Terminal und die von der Maschine dazu rückgemeldeten Ist-Daten, wie Mengen, Zustände oder Störungen, werden automatisch auftragsbezogen erfasst und gleichzeitig im ERP-System verbucht. Aufgrund der feinen Granularität – es kann jeder einzelne Takt automatisch verbucht werden – kann der Fertigungsverlauf sehr detailliert ausgewertet werden. Man bekommt dann Abweichungen in den Taktzeiten grafisch angezeigt und kann die Ursachen (wie z. B. geändertes Material oder Werkzeug) analysieren. Weiterhin können dem Werker am Terminal auch auftragsbezogene Zusatzinfos, wie Arbeitsanweisungen und Konstruktionszeichnungen, eingeblendet werden.
So haben alle Mitarbeiter in der Fertigung – vom Werker an der Maschine bis hin zum Abteilungsleiter – stets einen Überblick über den aktuellen Abarbeitungszustand von Fertigungsaufträgen. Unsere Erfahrung zeigt, dass dies auch ein nicht zu unterschätzender Motivationsfaktor ist.
Letztendlich bieten die automatisch von der Maschine gelieferten Unterbrechungsgründe nicht nur wichtige Zusatzinfos über den Fertigungsprozess, sondern können ggf. auch für eine vorausschauende Wartung genutzt werden. Es ist immer effizienter, eine Instandhaltung vorbeugend einplanen zu können, als dann von einem Ausfall überrascht zu werden. Und Sie wissen ja: ein Ausfall kommt immer dann, wenn man ihn am wenigsten braucht!
Feedback aus der Praxis
In der Praxis haben unsere Kunden ein exaktes, realistisches und absolut detailliertes Abbild ihrer Fertigungsprozesse. Nach der Installation der N+P-Lösung als Pilotprojekt an einer Engpassmaschine hat uns ein Produktionsleiter folgendes Feedback gegeben:
„Wir hatten schon immer das Gefühl, dass die Maschine wesentlich effizienter laufen könnte. Jetzt sehen wir die Wahrheit: Die Effizienz ist um 24 % niedriger, als auf Basis der manuellen Rückmeldungen bisher angenommen. Durch die detaillierten Taktzeitmeldungen haben wir jetzt schon 3 bis 4 Ansätze, die Effizienz der Maschine zu steigern.“
Fazit – Mehrwerte der Maschinendatenerfassung
→ Unternehmen sind in der Lage, Potenziale in ihrer Fertigung zu erkennen
→ Exakte Ist-Mengen und -Dauern werden in der Nachkalkulation berücksichtigt
→ Fertigungsprozesse sind durch Kennzahlen wie OEE (Gesamtanlageneffizienz) messbar und vergleichbar
→ Prozessdaten werden erfasst auf deren Basis ggf. Nachweißpflichten gegenüber Kunden erfüllt werden
Erfahren Sie mehr in unserem kostenfreien Webcast Produktionsdaten clever nutzen und vernetzen.